Оглавление
A brief discussion on the application of laser technology in industry
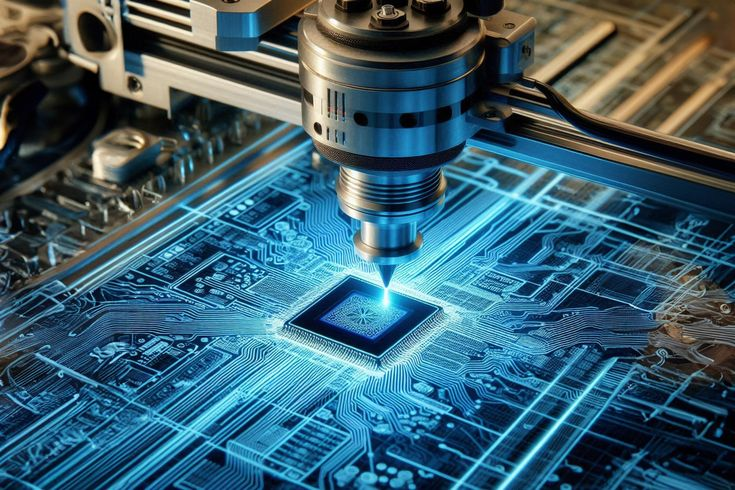
A laser is one of the very important instruments of modern industry, which creates unique advantages of precision, speed, and efficiency across a broad spectrum of fields. From cutting, welding, and engraving to the cleaning of parts, laser systems are replacing modern product manufacturing activities across industries.
The levels of manufacturing standards, coupled with increasing emphasis on automation, will continue to swell the applications of laser systems. This flexibility allows laser system applications in processing different materials within several sectors, such as automotive, aerospace and defense, electronics, and medical devices.
Laser systems are better alternatives in cost-effective and time-bound applications where the amount of material waste during the operations can be greatly reduced as compared to the old-fashioned tools. This article, therefore, attempts a concise coverage of laser technology in various industrial applications and its most likely promising position as a key driver for industrial innovation and development.
Part 1. What is Laser Technology?
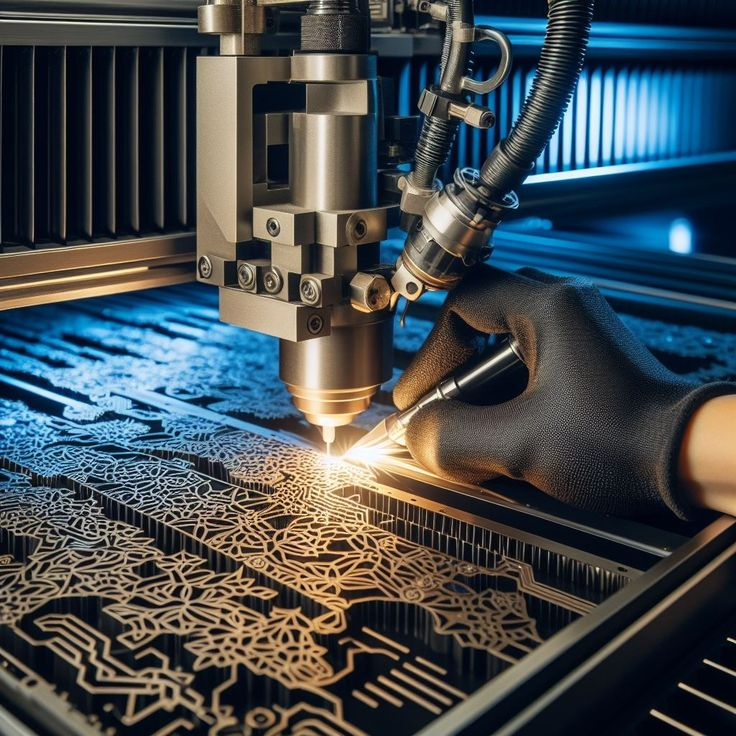
The basic idea behind laser technology is the creation and magnification of light by stimulated emission of radiation. The term “laser”, for instance, is for light amplification by the stimulated emission of radiation.
Unlike normal lights, lasers produce simple, coherent, brighter, and unidirectional beams of light. This special property of concentrating energy over a very tiny area makes lasers very suitable when working with technology that seeks very high precision and intensity.
The non-contact nature of laser processes means that there is no wear and tear on either tools or material, thus improving quality. The advancement made will see lasers becoming more powerful and efficient, thus going into the automation systems, making them a primary component in modern manufacturing and production.
Part 2. Application in Laser Cutting
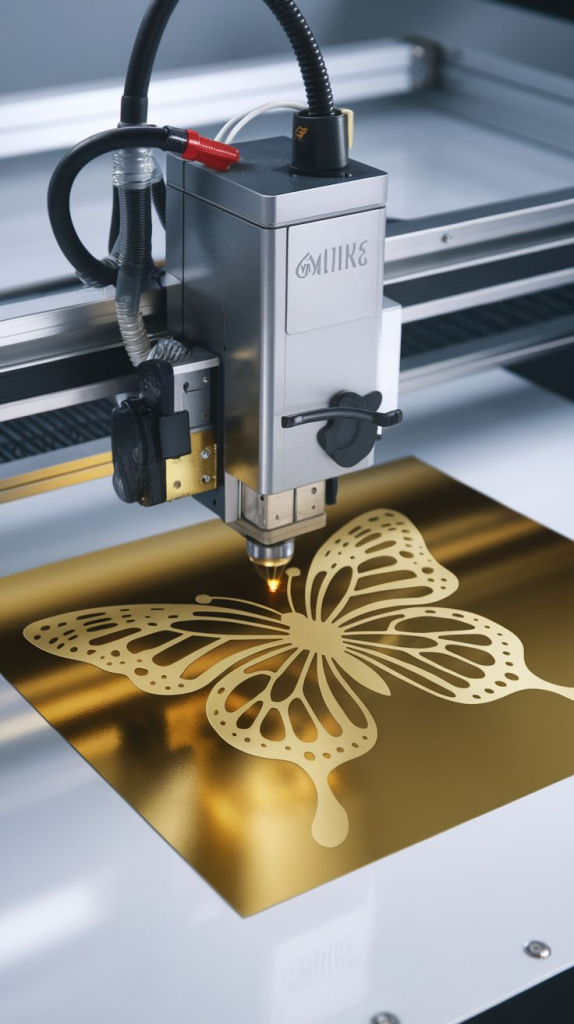
Laser cutting is among the most prevalent applications of laser technology in the industry. It is a major technique of high-powered and focused lasers for very precise cutting or engraving of materials.
In this case, a highly energetic laser beam hits and moves across the material, melting and vaporizing it. Usually, with the help of a stream of a gas like oxygen or nitrogen, the molten material is blown away, rendering a cut very clean and accurate.
One feature that makes laser cutting attractive is that it is precise; it produces shapes, edges, and very fine details with the least wastage of material. Such high precision results in less post-processing, with a concurrent saving of time and cost. It is also non-contact, meaning there will be minimal stress on the material and hence maintain integrity even on very thin components.
In addition, laser cutting is productive and indeed leads to the use of high-end CNC (Computer Numerical Control) Systems. This automates the complete process, delivers repeatability, and optimizes cutting patterns that are very complex. It thus qualifies as a process for a possible economic series.
However, there are certain limitations to laser cutting. Initial investment required is fairly hefty, and energy consumed could be substantial, especially when one is cutting thick or highly reflective materials.
Part 3. Application in Laser Welding
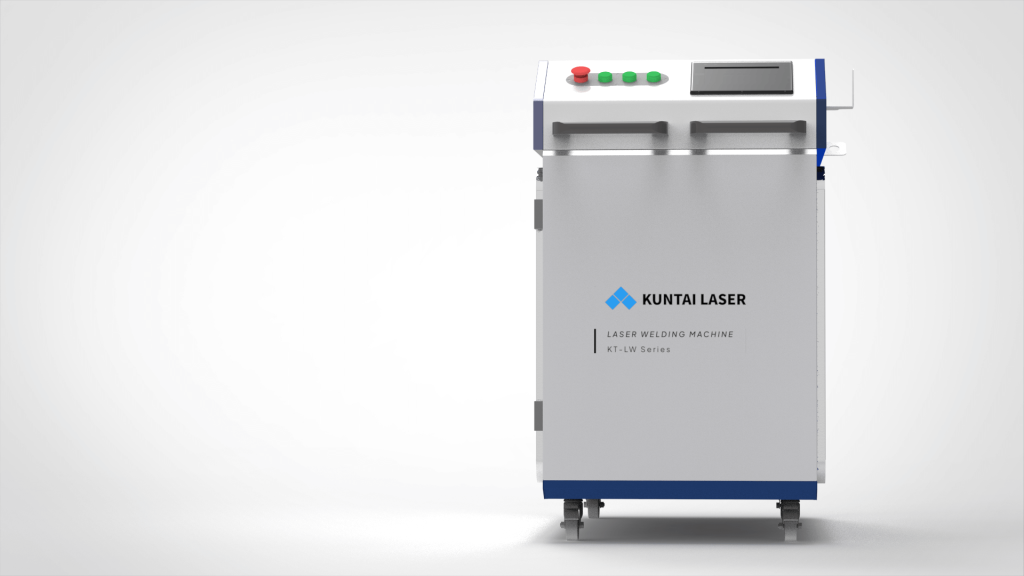
It is a highly skilled, yet very efficient, industrial process used to join metals or thermoplastics by welding through laser beam focus. The laser beam passes through the weld joint area, wherein, intense energy is applied to quickly melt the material in that zone; cooling and solidifying of this weld results in a clean and strong weld.
If one had to name a few advantages of laser welding, then nearly distortion-free deep and narrow welds within thick or inconspicuous zones would be one. This puts the laser welding in an inimitable position in such industries as automotive, aerospace, electronics, and medical device manufacturing, where product integrity and precision are of utmost importance.
For instance, car makers join body parts through laser welding to an extent that these joints are mechanically strong and capable of standing up to aesthetic considerations, while in the delicate sectors, electronics companies weld battery tabs and microcircuits.
Laser welding has its best performance at speed, automated production in continuous high volumes, and maintaining a constant level of welding quality if integrated with a robotic system and CNC machine. It suits those applications that demand speed impeccably. Moreover, this leads to minimal spatter, fumes, and post-weld cleanup, allowing for a safer working environment and less maintenance.
Another pros of laser welding is that it can weld different materials or metals thinner than any conventional method could weld. A heat source, such as the laser, can be applied with precision, so as to prevent warping or damage from heat on sensitive components.
However, to get it to work, a huge investment must be channeled into bringing it to the ground, while great attention must be paid during the alignment process of the workpieces to be joined. For very reflective materials, for instance, copper or aluminum, a consideration regarding laser wavelength and angle of incidence might have to be made to make sure that some success in absorption of the laser energy is achieved.
Despite these disadvantages, laser welding is preferred for advanced manufacturing due to the speed, strength, accuracy, and automation offered by it. Yet, with the evolution of laser technology, there is no doubt that all other efficient and flexible welding systems will be created to cater to the ever-growing demands of the modern industry.
Part 4. Application in Laser Marking
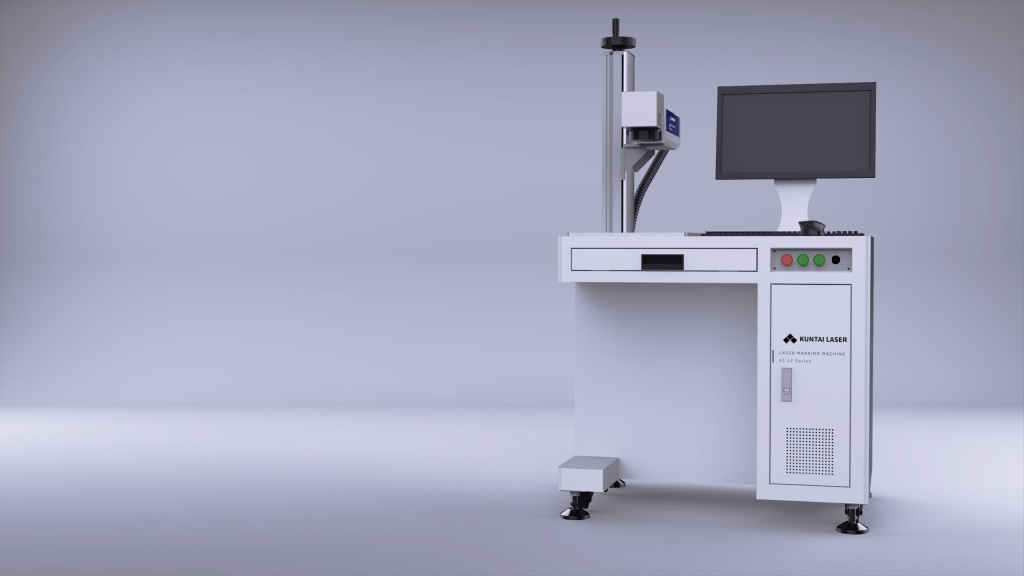
Laser marking is often sought after in many industries that deal with permanent, good-looking marks on a myriad of materials. Unlike more conventional printing or engraving techniques, the marking laser beam is kept in a narrow focus and physically lands on the surface of a product without even touching it.
It could impart any color of choice or remove a minute thin layer from the surface, or it could even texture the surface that stands facing it, all dependent on the material at hand and the marking methodology selected.
Different types of laser marking techniques exist.
- Annealing: Also referred to as heat tinting, this method is most commonly used on stainless steel and causes a color change due to localized heating without actually removing material.
- Etching and Engraving: The surface is removed superficially in these methods to form somewhat permanent marks or deeper ones.
- Foaming: The raised mark is produced in thermoplastics where the surface melts, releasing gas bubbles.
- Color Change: Changes the chemical structure of certain materials, mostly plastics, to obtain high-contrast markings.
Laser marking has its benefits. It is fast and precise, capable of creating very minute marks without harming the material. Also deemed environmentally friendly, as no inks, solvents, or acids are required for its processing.
Yet the initial installation of laser marking systems might be costly, and some materials may require special lasers. Highly reflective or transparent surfaces, for instance, might require some pre-treatment or lasers not usually used in standard applications.
Even with this, the advantages far outweigh the disadvantages, especially where industries require product traceability and quality assurance. As the industries continue to embrace automation and sustainability, the keyword laser marking is becoming more and more relevant in modern manufacturing processes.
Part 5. Application in Laser Cleaning
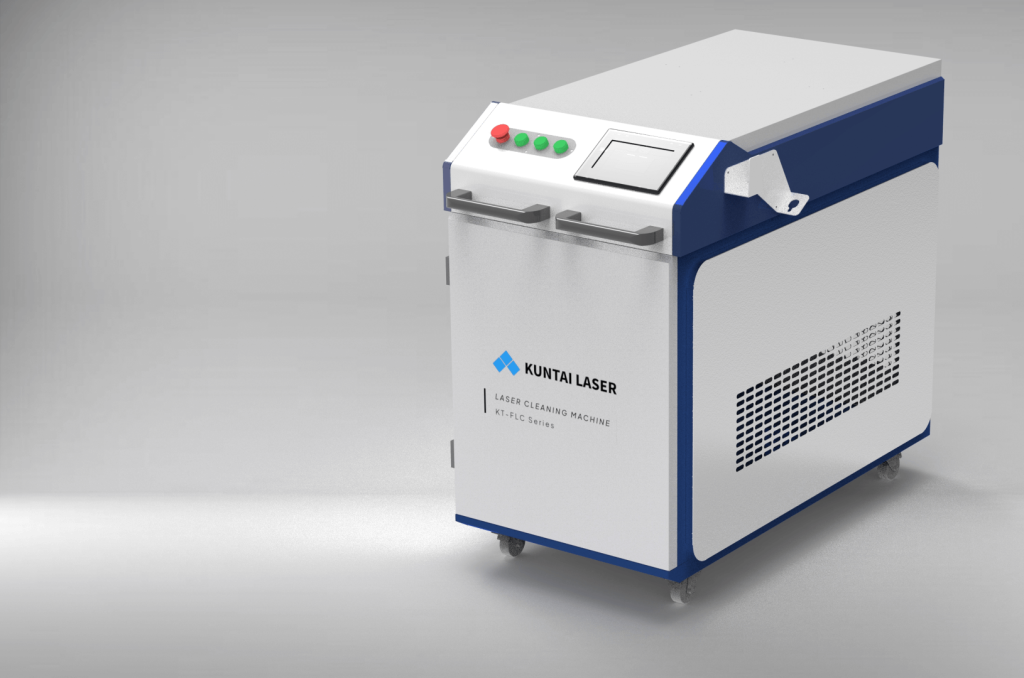
Laser cleaning is a finishing technology so advanced and green that it is employed to cleanse surfaces while removing contamination, coatings, rust, paint, grease, or any oxide layer without resorting to chemical or abrasive treatments. The concentrated laser beam hits whatever surface coating lies there and vaporizes it or forces it out violently due to immediate heating and expansion.
Laser cleaning finds applications in aerospace, automotive, shipbuilding, electronics, power generation, and conservation of heritage. Since laser cleaning involves thin-layer cleaning of stone, metal, or artworks without causing the original materials any harm, conservation of heritage is one of the domains where it is hugely popular.
One of the greatest advantages of laser cleaning is that it is environmentally friendly. No chemicals and no disposal of chemical waste meana lesser environmental impact concerning waste disposal.
Another important aspect to consider is that laser cleaning is also highly selective and controllable. By controlling laser parameters such as power, pulse duration, and repetition frequency, operators can remove specific layers or contaminants without impairing the base material.
Part 6: Advantages and disadvantages of laser technology
Преимущества
- High Precision and Accuracy: Laser processes possess excellent precision in the design and cutting of highly complex shapes, which is often not possible with traditional instruments. This is especially so where great tolerances are required, for instance, electronics, aerospace, and medical device industries.
- Non-Contact Process: Due to the operations being non-contact, there is generated very little mechanical stress on the workpiece material. This greatly reduces deformation, wear, or contamination risk and ensures uniform results, regardless of delicate or thin material.
- Speed and Efficiency: Laser systems can perform tasks at much greater speeds than conventional means. Integration of laser machining operations with CNC or robotic automation is identified as bringing very high throughput, hence being highly suitable for mass production.
- Versatility: Lasers can cut metals, plastics, ceramic, glass, textile, and even organic materials. The same system is commonly moved between different applications with minimal changeovers required.
- Green Process: Laser-specific operations can be a greener alternative to chemical or abrasive techniques, especially for cleaning and marking applications. They produce less wastes that go into landfills while minimizing the dependence on consumables and are beneficial to workers and the ecosystem.
- Low Maintenance: Modern laser systems have a lot of reliability with fewer moving parts and low maintenance needs as against the mechanical ones that would increase downtime and operating costs.
Disadvantages
- High Initial Expense: Among the main drawbacks associated with the laser process is the price of installation and equipment. This investment might be a serious barrier for small or low-volume establishments.
- Energy Consumption: While lasers are considered to be safe from the point of view of energy consumption, very high-powered systems can consume a huge amount of electricity, especially when working with thick materials or reflective surfaces.
- Вопросы безопасности: Laser beams, especially those emitted by high-powered setups, can cause severe damages to eyes and skin of the operators. Thus proper shielding and safety measures are of utmost importance.
- Material Limitations: Some materials, like reflective or transparent surfaces, can be difficult to process using normal lasers and require specialized equipment.
Part 7. The Future Development Direction of Laser Technology in the Industrial Field
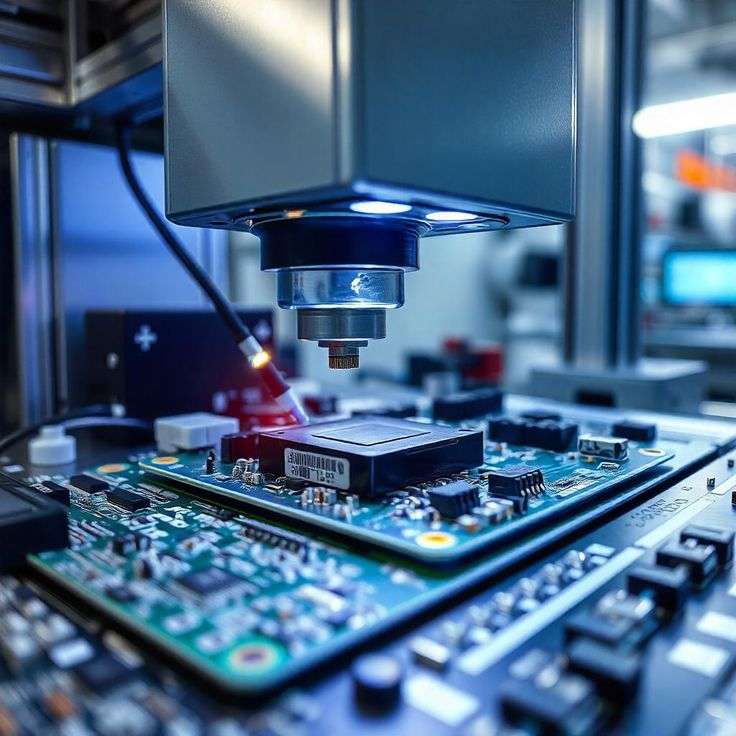
The future of laser technology in the industrial sector witnesses significant growth and innovation. In a future where factories are smarter and faster, with a focus on sustainable manufacturing, lasers will increasingly be called upon to bring enhancements in levels of productivity and precision.
Integration with automation and AI is a trend that will majorly shape the future of laser technology. Thus, smart laser systems having real-time sensors and AI-based controls are going to allow companies to have adaptive and autonomous manufacturing processes.
A trend towards further miniaturization and portability of laser equipment is now being observed. The compact and mobile laser systems ease the use of laser technology in confined areas or in field conditions such as shipbuilding or aircraft maintenance.
The environment is yet another major orientation for manufacturing processes. With a regard for industries minimizing environmental impact, laser cleaning and marking are becoming greener alternatives to chemical and abrasive methods. Energy-efficient lasers and systems with smaller carbon footprints are being created to mark stricter environmental standards.
Conclusion
As regarded by one and all, lasers are among the great inventions of modern times concerning precision, speed, and application diversity. With laser energy, no manufacturer cares to waste raw materials for the best quality in dealing with various products.
With changes in automation systems and the environment, laser technology will gain more emphasis in industrial manufacturing. Leveraging these technologies, industries can realize efficiency, a greener approach, and global competition in a quickly changing environment.