Tabla de contenido
How to Choose the Right Laser Cleaning Machine for Your Factory?
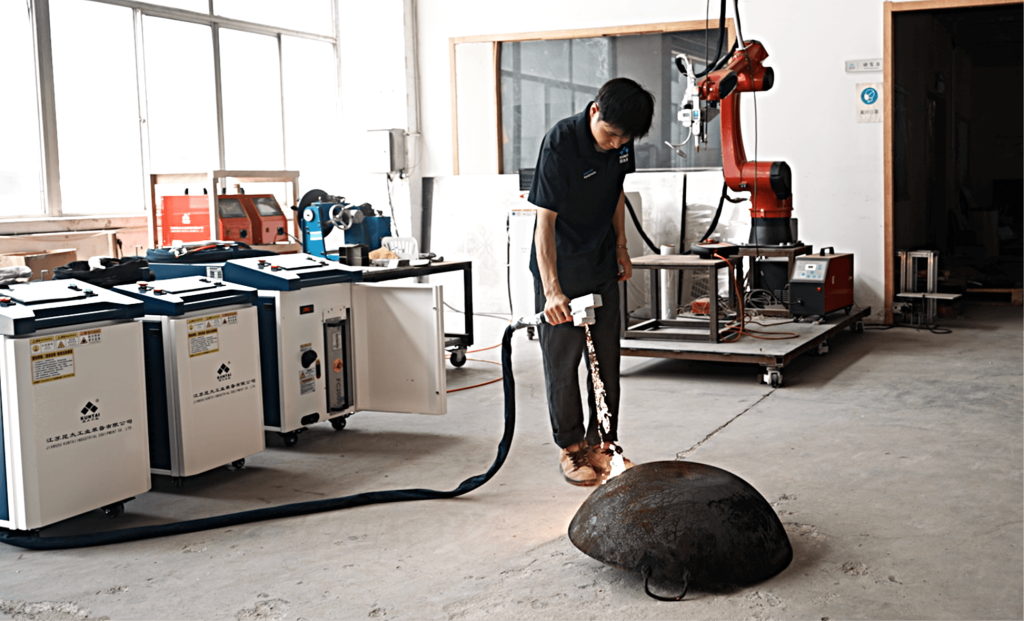
In this rapidly industrializing world, keeping surfaces clean, free of rust, and being appropriately prepared is crucial to efficiency, product quality, and safety. Conventional cleaning systems either ruin the material, take time, or pollute the environment.
This is where laser-cleaning technology provides an efficient, precise, and environmentally safe alternative. With so many varieties of laser-cleaning machines differing in power and features, how does one choose one for the factory?
This is not just a question of selecting the most powerful machine; it is one of matching the proper specifications, features, and design with your unique requirements and production goals. This guide will take you through everything you need to know about these cleaning systems, starting with their working principles and ending with an understanding of some key specifications.
Part 1: What is a laser cleaning machine?
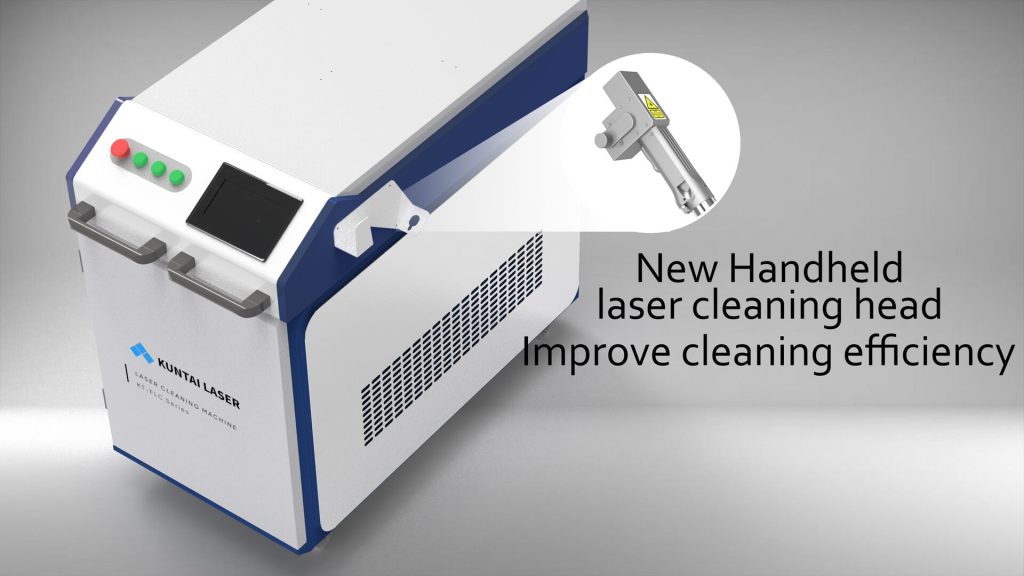
Laser cleaning is the advanced industrial design of surface cleaning using high-intensity laser beams to remove chemical coatings, rust, or residues. It will never cause any structural damage to the material being cleaned.
In contrast to conventional cleaning techniques, such as sandblasting and chemical solvents, laser cleaning is a distinguished case. These processes are non-contact, precise, and environmentally friendly.
Highly focused or concentrated forms of laser energy are directed toward unwanted layers that tend to absorb the energy and, for that reason, vaporize or blow off through micro-explosion effects.
Designs for laser-cleaning machines vary. They may be classified as handheld, portable, or fully automated systems. Cleaning using lasers is mainly applied in automotive, aerospace, shipbuilding, electronics, and art restoration.
Part 2: Working principle of the laser cleaning machine
The operating principle of laser cleaning equipment is that the laser energy interacts with surface impurities, which are then washed away. The high-intensity laser beam, when it falls on the contaminated surface, targets the trapping of unwanted material and releases it without harming the base substrate.
The process is classified into two main physical phenomena:
1. Laser Ablation
When a laser beam falls on the surface, since contaminants absorb the energy more quickly than the underlying material, they tend to evaporate or sublime due to the intense heating that follows. Here, the unwanted layer is lifted away successfully without affecting the original exposed grain.
2. Thermal Expansion and Shockwave Generation
In pulsed laser cleaning, rapid heating gives rise to sudden expansion in the contaminant material. Such thermal expansion brings about shockwaves and these help dislodge and eject particles from the surface. This is particularly useful for removing rust, paint, or other thin coatings.
The key aspect of laser cleaning is having total control over the parameters of the laser itself:
- The wavelength:Different materials absorb laser energy at different wavelengths. Thus, the most suitable wavelength has to be chosen for efficient laser work.
- Pulse Duration:Short pulses limit heat transfer to the substrate, and hence limit the likelihood of thermal damage.
- Energy Density (Fluence): Amount of energy delivered must be enough to overcome stickiness of contaminants without damaging base material.
Laser cleaning is a very carefully controlled, non-contact process, which is appropriate for very delicate or sensitive surfaces. It generates minimal waste, usually only vaporized material and a few microscopic particles that can be gutted effectively.
It eliminates the need for any abrasive media, chemicals, or physical force and thus reduces the maintenance requirements and risks to environment because it cleans without contact. Thus, it is advantageous with precision to clean those industries, materials of which are mostly retained, as in aerospace, electronics, and heritage conservation.
Part 3. How to Choose the Right Specifications for Your Laser Cleaning Machine?
However, as mentioned, the laser cleaning requirement has to go through a few criteria to match the kind of cleaning tasks and goals you have headed for your operations.
1. Laser Power
Certainly among the criteria, the major is the ‘Laser Power’ which is normally measured in watts (W).
- Low-power laser: 50W-200W suitable for light removal cleaning activity, such as delicate cleaning for rust removal or cleaning fragile surfaces.
- Medium range, around 200W-1000W, performs cleaning at a faster rate, and can be used in the industrial level where heavy rust, oil, or coatings need to be removed.
- Heavy dutycleaning will be applied on the ship hulls and large metal structures as well as production equipment using high-power lasers of 1000W-3000W and above.
Increasing the power would increase cleaning speed, but higher costs and energy consumption would be involved. Pick a suitable level of power considering speed, cost, and precision for the application.
2. Pulse Type
Continuous wave (CW) and pulsed lasers operate according to your cleaning requirements:
- Pulsed lasers pulse high energies in very short times, such that heat damage becomes minimal. That’s why pulsed lasers are excellent for precision cleaning.
- Continuous wave lasers emit a constant beam, thus making these lasers more useful for the bulk removal of material, wherein thermal damage doesn’t matter.
3. Beam Delivery and Scanning System
An intense effect will be determined by its scanning width and beam delivery system in terms of specific areas at a time and the extent to which the machine can be adjusted for complex surfaces.
Speed clean-up will be ensured by having a larger scan area, while flexibility regarding different shapes and sizes will be ensured by using adjustable or programmable scanning heads.
4. Mobility and Portability
Portable, handheld laser cleaning machines are useful for factories that perform cleaning in various locations. On the other hand, stationary or robotic-integrated systems best provide cleaning for automated production lines.
5. Cooling Mode
Because lasers produce a lot of heat, these cooling units are generally necessary:
- Air-cooled: it is common for machines with lower power.
- Water-cooled systems: Used for medium- to high-power lasers designed to remain stable for long operations.
Part 4. What Special Features Will You Use in Laser Cleaning Work?
Crucial machine features can greatly differentiate the performance, efficiency, and user experience of a laser cleaning machine. The latest laser cleaning machines have been equipped with contemporary options for improving cleaning quality and expanding operational applications.
Here are some key special features to consider:
1. Adjustable Power and Frequency
In some laser cleaning machines, the user holds the ability to adjust the laser power, pulse frequency, and pulse width. Being able to adapt these parameters will ensure proper cleaning performance on a plethora of materials and contaminants.
The settings can be lowered to safely remove fine residues, which may involve no harm done to the base material, or the power may be ramped up for heavier-duty jobs.
2. Auto-Focus and Smart Scanning
The high-end laser cleaners have automatic focusing systems and intelligent scanning heads. Auto-Focus guarantees that, while the laser cleans uneven or intricate surfaces, it stays at a proper distance from the surface for optimum efficiency.
With Smart Scanning Patterns, the user can select diverse cleaning modes like spiral, line, or area scanning for better control.
3. Multilingual LCD Touchscreen
The user-friendly interface improves the whole experience. Equipment with a touchscreen and multilingual support allows modification of parameters, monitoring of system status, and troubleshooting without the need for specialized training.
4. Built-in Dust Collector Systems
Laser cleaning has become widely recognized as a possible source of ultrafine dust and vaporized particles. A built-in dust extractor or fume filter is required on the machine to keep the working environment clean and to ensure that the health of operators and sensitive equipment is protected.
5. Safety
Laser-cleaning machines must have sets of safety protection features: emergency stop buttons, key switches, laser safety shutters, and warning alarms. Some models also include an automatic shutdown feature when unsafe operating conditions are detected, which protects both the operator and the rest of the workplace.
Part 5. What type of products do you need to clean with a laser cleaning machine?
Laser cleaning machines are universal machines that can run through different fields of cleaning for different products. These are used for removing rust, paint, oil, oxides, and other contaminants without damaging the underlying material and are the most competent machines for very delicate applications as well as heavy-duty applications.
Products that can be cleaned using laser machines include:
1. Metal Surfaces
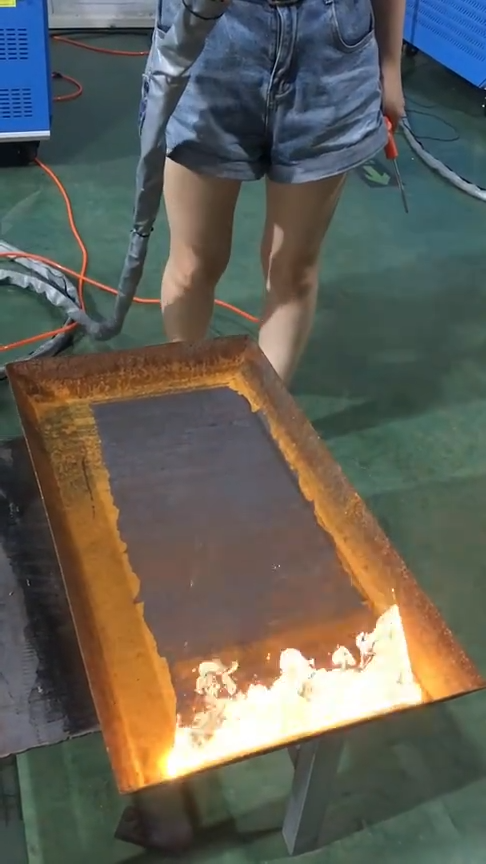
Laser cleaning, one of the most used types of cleaning, is that on metals- steel, aluminum, copper, and titanium. Use in industries provides laser cleaning for removing rust and old paint, oxides, and even coatings on these metals before welding, painting, or assembling.
2. Molds
Rubber molds, tire molds, and plastics injection molds often pick up residues affecting product quality. Laser cleaning is a non-abrasive cleaning process in that it cleans those without surface wear, thus enhancing their life and ensuring consistent quality of production.
3. Automotive Parts
Most automotive manufacturers use laser cleaning in surface preparations for bonding, welding, or painting. Automotive parts that benefited from this technique are engine parts, frames, and wheels, under the precision cleaning employed to achieve strong bonds and smooth finishes.
4. Aerospace Components
Laser cleaning processes used in the aerospace domain are critical for contaminant elimination, such as oxides and coatings on sensitive materials, including aluminum and composites. This process has an efficiency of part integrity and performance in service applications without imposing mechanical stresses.
5. Electronics
Laser removal of thin films, oxides, or adhesives from delicate electronic components can be done by this technology during manufacturing or repair processes. It serves as a means of precise and damage-free cleanness.
6. Shipbuilding and Railways
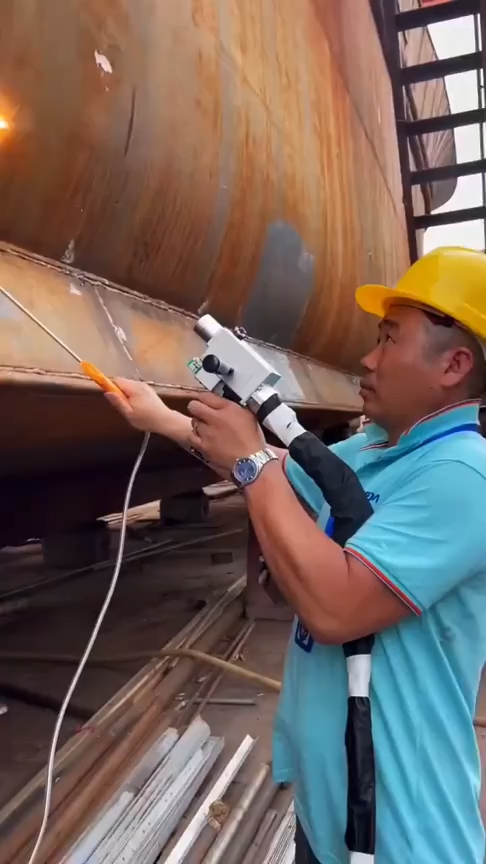
Shipbuilding and Railways are major structures that corrode and degrade their coating. Laser cleaning machines operate efficiently to clean without the use of sandblasting or chemicals over wide areas, thereby saving time and making it an environmentally friendly way.
Part 6: The top ten laser cleaning machine companies
Choosing a laser cleaning machine from a reputable manufacturer means the quality, performance, and after-sales support are up to a certain point. Here comes the top ten companies you can rely on in the laser cleaning machines industry:
1. Kuntai Laser (Our Recommendation)
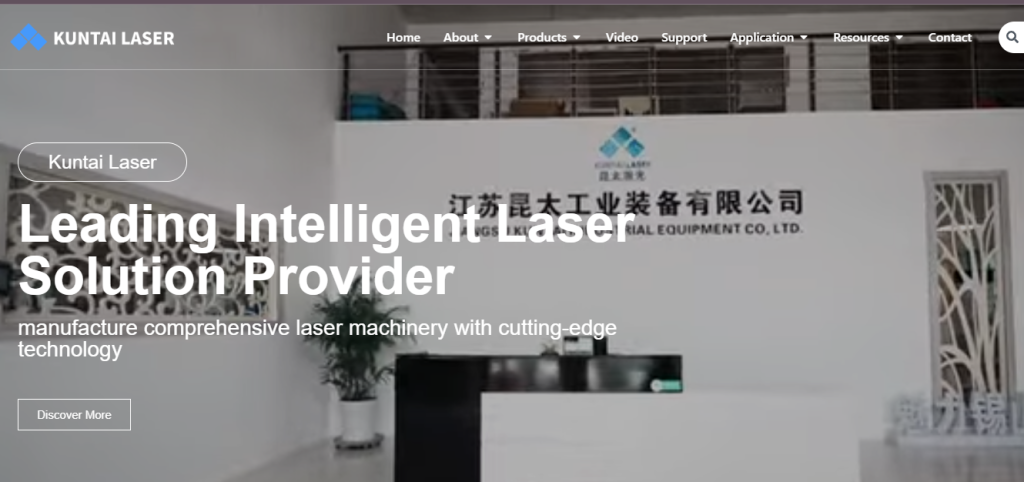
Láser Kuntai is a professional manufacturer of advanced laser cleaning machines for a whole range of processes such as rust removal, paint stripping, surface pretreatment, and more.
An aware source of innovation, high-quality manufacturing, and extraordinary customer service, Kuntai Laser provides custom-built machines for many industries, such as automobile, aerospace, and shipbuilding.
2. Trumpf
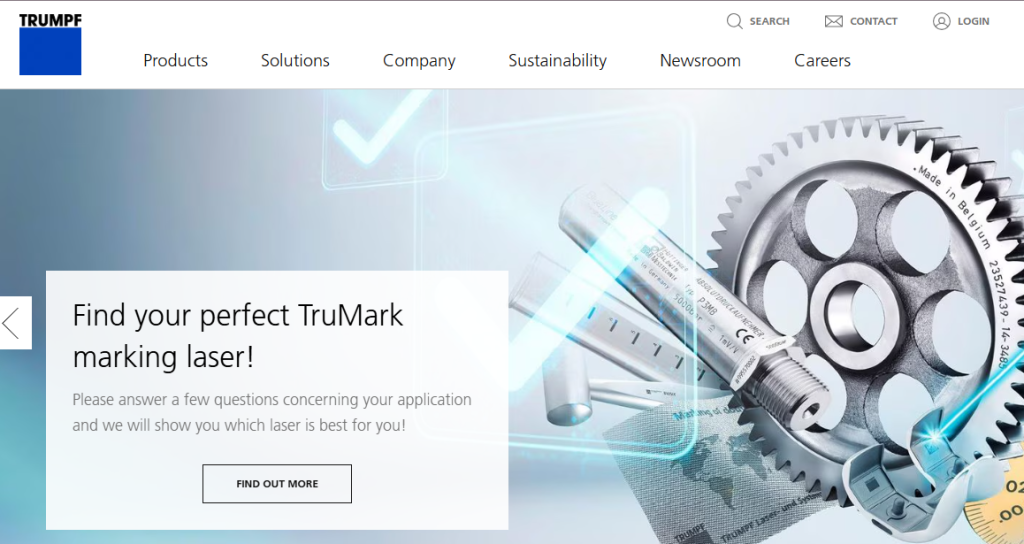
Trumpf is the name that speaks it all globally for laser technology. Excellent quality, high precision, and the most robust machines are what make up their laser cleaning machines.
3. Laser Photonics
Laser Photonics is a manufacturer of industrial laser cleaning equipment located in the USA. Portable and stationary devices have been designed for heavy manufacturing, defense, and aerospace.
4. CleanLaser (CleanLASER Systems)
From Germany, CleanLaser devoted itself to high-quality laser cleaning systems suitable for industrial as well as conservation purposes. Their systems can be used very well in the automotive sector and with heritage conservation.
5. IPG Photonics
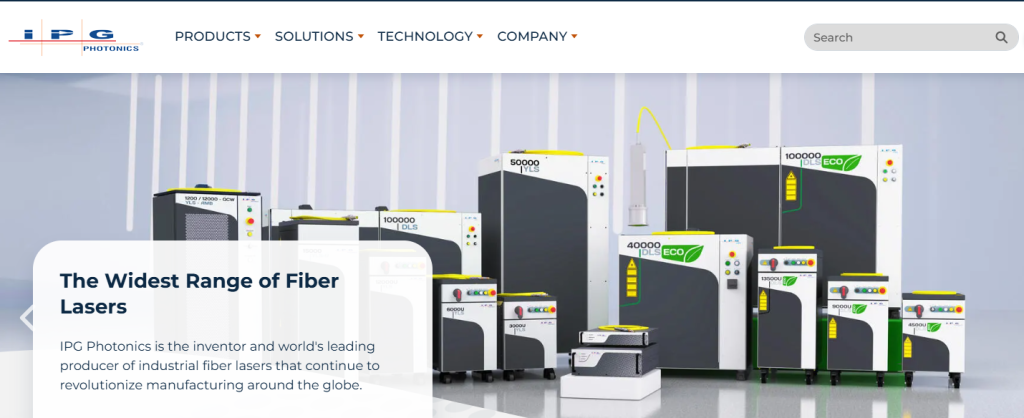
Fotónica IPG is the renowned manufacturer of high-power fiber lasers, which also produces laser cleaning systems. Its machines are known for their energy efficiency and longer service lives, thereby being consistent performers throughout their existence.
6. P-Laser
P-Laser provides compact-grade laser-cleaning solutions of an industrial standard. The systems are designed for easy incorporation into automatic production lines, as well as manual operations.
7. Coherent, Inc.
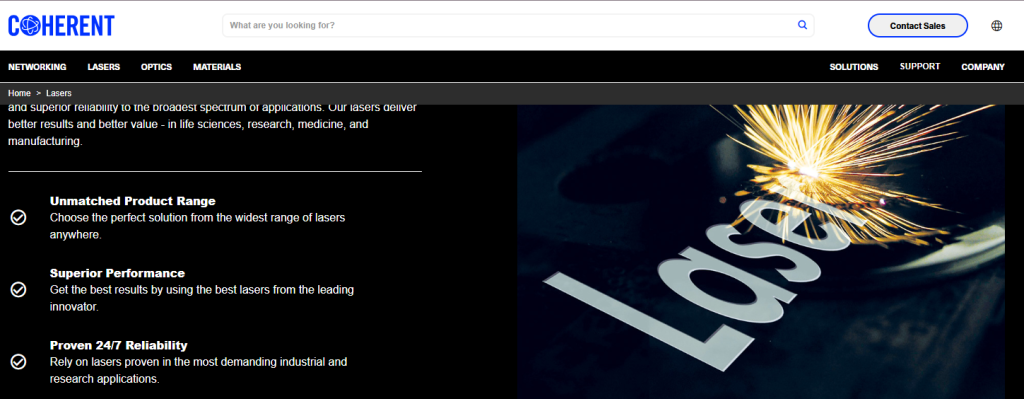
Coherent is a major force in laser technology globally; through a broad portfolio of laser cleaning solutions, these are tailored for various industries with precision and efficiency in mind.
8. Han's Laser Technology
As one of the top laser equipment manufacturers from China, Han’s Laser has a whole line of laser cleaning machines that offer high power and are affordably priced for industrial-scale operations.
9. XT Laser
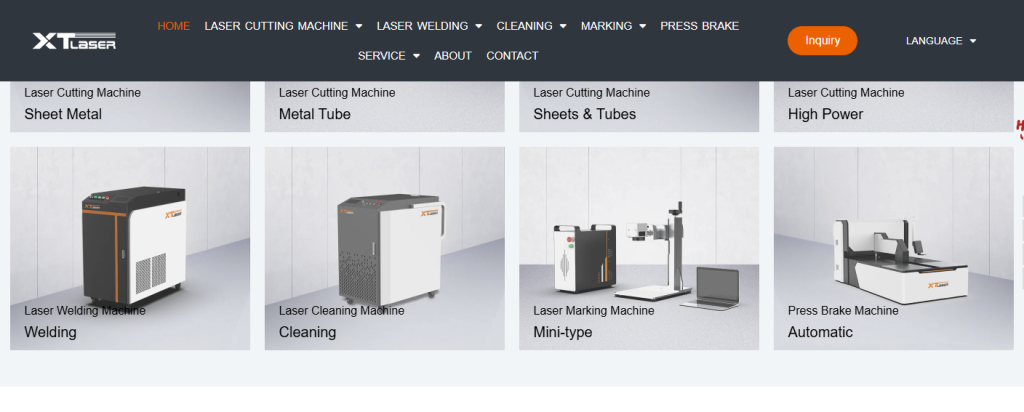
Focusing on affordability but high-performance laser cleaning systems, XT Laser is also recognized for providing flexible solutions to small and medium-sized companies.
10. SCANLAB
SCANLAB specializes in fiber laser solutions, including cleaning machinery known for delivering precision and reliability in highly demanding environments.
Conclusion
Picking an appropriate laser cleaning machine for your factory becomes a decision you would make once, but very crucial as it can be a significant difference in productivity, quality of products, and even efficiency in operations.
However, understanding how laser cleaning works, what specifications and special features to consider while purchasing such a machine, and the types of products to clean should help you in making a smart investment tailored to your specific needs.
In addition to this, the right choice of a manufacturer from whom to purchase the affordable and well-matched equipment with a great after-sales service is another important factor. Kuntai Laser has such kinds of solutions, advanced designs for your industry’s needs.